
Subscribe To Receive Updates More Blogs!
In an ever-evolving and increasingly competitive world, organizations are seeking ways to distinguish themselves and achieve sustained growth. Developing a culture of continuous improvement, where the relentless pursuit of doing things better and innovation becomes an integral part of the company’s DNA, might be the key to realizing such coveted growth.
However, building an improvement culture is no simple task. It demands commitment, effective leadership, and robust management practices. This journey involves transforming mindsets, crafting programs, and implementing processes that propel the organization toward excellence.
To cultivate a genuine culture of continuous improvement, getting management commitment, employee engagement – equipping and encouraging their active participation -implementing processes that underpin improvement, and aligning organizational strategy with continuous improvement objectives are all vital.
By embracing these principles and practices, companies will be on the right track to achieve sustained growth, remaining competitive in a dynamic and challenging marketplace.
What is a Continuous Improvement Culture?
A continuous improvement culture refers to an organizational environment where the relentless quest for improvement, innovation, and excellence is deeply rooted and valued by every member. It promotes the mindset that there’s always room for improvement, and everyone plays an active role in identifying and solving problems.
As part of the corporate culture, continuous improvement becomes an ongoing process integrated into the organization’s daily activities. Employees are encouraged to challenge the status quo, suggest ideas, and implement improvements. Continuous learning and development are valued, and mistakes are seen as growth opportunities.
Such a culture demands commitment from the entire organization, from top management to operational areas. It offers numerous benefits, such as increased efficiency, cost reduction, improved quality and customer satisfaction, employee motivation, and business growth. It also fosters an adaptive and innovative mindset, making the organization more resilient in the face of market changes and ensuring long-term corporate sustainability.
The Principles of a Continuous Improvement Culture
A continuous improvement culture should be grounded in KAIZEN™ foundations that guide actions and decisions within the organization. These principles should steer the behaviours of the entire company. Let’s delve into five of these core principles:
1. Create Value for the Customer:
The primary objective of a continuous improvement culture within an organization is to create value for the customer. This involves listening to the customer’s voice and understanding their needs and expectations. The company should also adopt a “quality-first” mindset, striving to deliver products and services that meet or exceed customer expectations while continually enhancing the buying experience.
2. Create Flow Efficiency:
This principle focuses on creating workflow efficiency. It includes reducing waste and eliminating non-value-adding activities. Continuous improvement aims to implement actions to enhance flow efficiency, ensuring workflows are effective without interruptions. Adopting a “pull” approach, where production is based on actual customer demand, is vital, avoiding unnecessary stock and overproduction issues.
3. Be Gemba-Oriented:
The term “Gemba” refers to the place where real work is done and value is added. This principle underscores the importance of going to the Gemba to identify, understand, and address problems from the root cause. The continuous improvement culture encourages leaders and employees to be physically present at the Gemba, gather data, and take effective corrective actions. Standardizing processes to create consistency and predictability in operations is also essential.
4. Empower People:
Continuous improvement recognizes that people are a valuable asset. This principle emphasizes the importance of empowering and developing high-performing teams. This involves providing training, tools, and resources to enable employees to contribute to improvement actively. Moreover, it’s essential to set team goals aligned with the organizational strategy and foster a work environment where the principle of “no blame, no judgment” is deeply rooted, promoting continuous learning and collaboration.
5. Be Scientific and Transparent:
This principle is based on the importance of addressing challenges in a data-driven, scientific manner. Continuous improvement encourages long-term thinking and planning actions aimed at sustainable results. Speaking with data, seeking evidence, and objective information to support decision-making is crucial. The PDCA and SDCA (Plan-Do-Check-Act/Study-Do-Check-Act) frameworks are employed to plan and implement actions. In a culture of continuous learning, mistakes, and challenges are seen as growth opportunities.
These five continuous improvement principles provide a robust framework for establishing an organizational culture focused on operational excellence, customer satisfaction, and sustainable growth.
What Are the Steps to Implement a Continuous Improvement Culture?
Implementing a Continuous Improvement culture requires the development and execution of several programs that should run at the same time:
1. TRANSFORMATION KAIZEN™: Managing the Socio-Technical Transformation Program
This program focuses on managing the social and technical aspects of implementing a KAIZEN™ culture and ensuring its sustainability. It involves implementing a structured process to facilitate quick and successful transformation. The program includes activities like coordinating improvement efforts, training employees in improvement principles and methodologies, coaching natural team leaders, sharing best practices, and fostering a culture that reinforces positive behaviours.
2. Daily KAIZEN™️: Change Behaviors and Culture
The Daily KAIZEN™️ program aims to drive organizational behavioural and cultural changes. It involves developing continuous improvement principles and problem-solving capabilities in natural teams, including leaders and their members. This program encompasses practices like regular meetings or sessions to discuss improvement opportunities, empowering employees to identify and address problems, and fostering a collaborative and proactive mindset.
3. VALUE STREAM KAIZEN™: Implement World-Class Benchmarks
This program focuses on driving process improvement through KAIZEN™ projects and events. It aims to achieve world-class results by implementing best practices in the value chain. It involves analyzing the current value flow, identifying areas for improvement, and executing targeted projects and events to eliminate waste and enhance overall performance.
4. STRAT KAIZEN™: Secure Management Commitment
This program seeks to secure management’s commitment to organizational transformation and create a genuine continuous improvement culture. It involves defining and implementing innovative strategic objectives, promoting a countermeasure culture, and leading by example. This program aims to align organizational leadership with transformation efforts, ensuring their active involvement and support throughout the entire process.
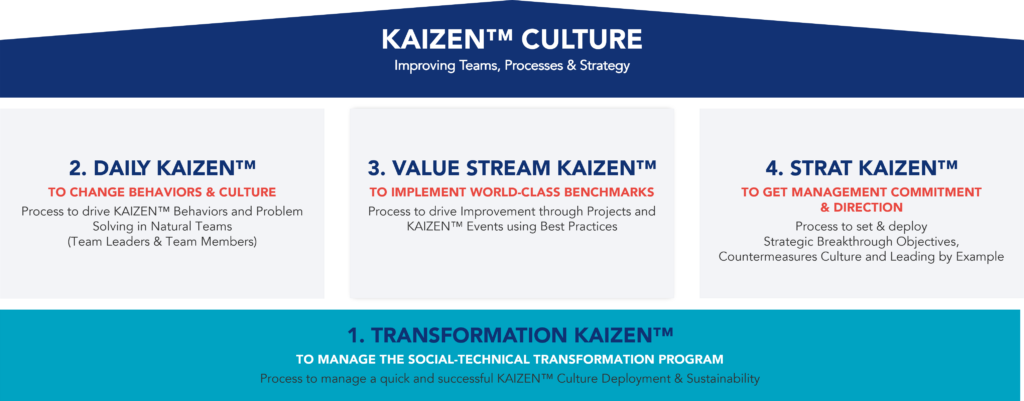
The duration of a Lean Kaizen Transformation to implement a genuine improvement culture can vary based on several factors, such as size, complexity, availability, and specific organizational objectives. It generally lasts around three years, but developing a customized roadmap based on the organization’s unique circumstances is essential to ensure successful transformation. The following image shows a macro plan for implementing a continuous improvement culture.
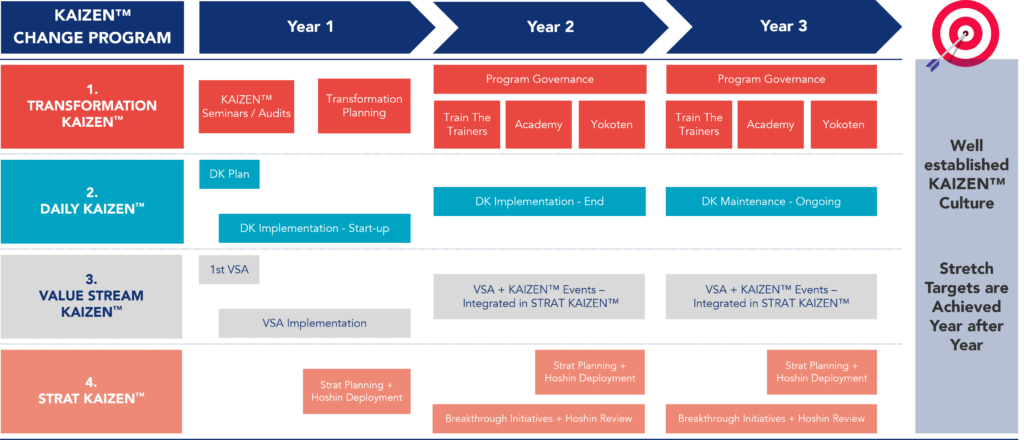
The Role of Organizational Levels in Implementing a Culture of Continuous Improvement
To implement a continuous improvement culture through these four programs, involvement from all organizational levels is needed. Each group plays one or more pivotal roles in implementing and preserving this culture.
The KAIZEN™ Office takes responsibility for the Transformation KAIZEN™ program. Coaches train and guide top management and Gemba teams, providing them with the tools and techniques required to drive continuous improvement. Moreover, they coordinate improvement efforts, conduct specific pilots, and share knowledge and best practices, ensuring that learning is spread throughout the organization.
At the management level, top managers and team leaders play an important role in implementing continuous improvement. Project teams are led by managers in charge of the Value Stream KAIZEN™, learning to plan and implement tangible process improvements. They are also called upon to lead KAIZEN™ events – short workshops with specific improvement objectives. Projects are typically conducted in 3 to 6-month sprints, allowing an agile approach to achieve measurable results.
Furthermore, management teams are responsible for Strat KAIZEN™, which involves committing to continuous improvement behaviour and leading by example. Through the Strat KAIZEN™ program, these teams define innovative objectives and support implementing the organizational strategy, ensuring continuous improvement aligns with company goals and objectives.
Finally, at Gemba’s natural team level, team leaders and their members are responsible for implementing the Daily KAIZEN™ program. These teams should identify daily improvement opportunities and implement actions to address immediate problems. The team leader plays a pivotal role in training and coaching team members, developing their skills, and continuously encouraging them to seek operational excellence. In summary, various organizational levels play essential and complementary roles in a continuous improvement culture.
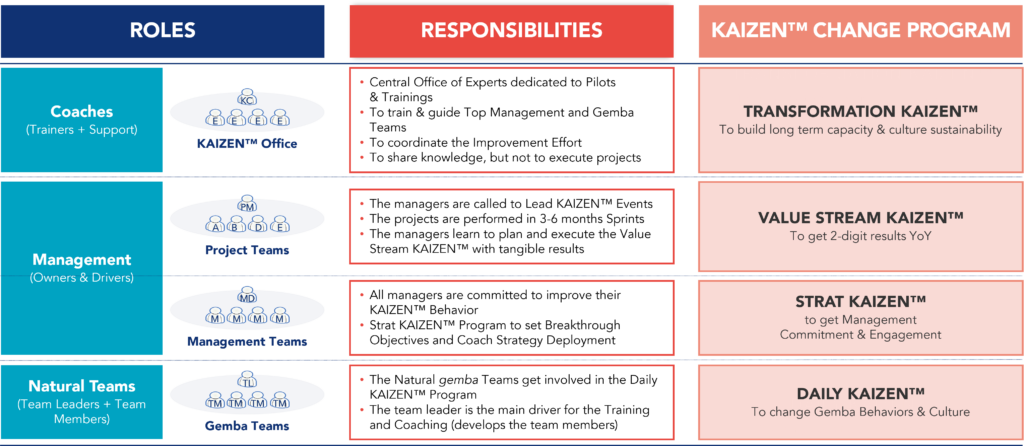
Main Challenges in Implementing a Culture of Continuous Improvement
Developing a continuous improvement culture enables companies to drive organizational success, but many implementations face challenges and fail to achieve expected outcomes. Some reasons for this include a lack of top management commitment, a limited view of continuous improvement, seeing it as a toolkit rather than a socio-technical system, a lack of leadership knowledge and development, and a lack of commitment from the organization as a whole. To ensure successful implementation, it’s necessary to secure top management commitment, foster a continuous improvement mindset throughout the organization, establish an effective communication model, define priorities and plan initiatives, and have an effective way of measuring their impact on key indicators.
By adopting these countermeasures, companies can overcome challenges encountered during organizational transformation and achieve positive outcomes.
The Power of Continuous Improvement Consulting
Consulting plays a pivotal role in implementing a corporate culture of continuous improvement. Consultants bring specialized knowledge and practical experience, providing guidance and support throughout the transformation process.
Some of the main advantages of organizations turning to consulting firms to implement a culture of improvement are:
1. Diagnosis and Assessment:
Consultants comprehensively diagnose the organization’s needs, evaluate the existing culture, processes, and management practices, and identify improvement areas.
2. Strategy Design:
Based on the diagnosis, consultants assist in developing a future vision and a clear, comprehensive strategy for implementing a continuous improvement culture. They also define objectives and key performance indicators to direct the improvement effort.
3. Planning and Implementation:
Consultants assist in planning and implementing initiatives. They help identify the best approaches and methodologies, develop action plans, set milestones, and define responsibilities. They also provide support and coaching in implementing improvement projects, helping overcome obstacles, and ensuring alignment with the organizational strategy.
4. Training and Coaching:
Consultants develop specific training programs, conduct workshops, and provide resources to ensure all organizational levels possess the knowledge required to contribute to the continuous improvement culture effectively.
5. Continuous Monitoring:
Consulting aids in implementing continuous measurement and assessment systems to track the progress and outcomes of initiatives. They also help establish performance indicators, set standards for follow-up meetings, conduct data analyses, and provide feedback to the organization on progress. Based on these insights, continuous strategy and approach improvements can be made to maximize the benefits of continuous improvement.
6. Change Management:
Lastly, consultants are crucial in change management throughout the cultural transformation process. They assist in communicating the importance of change, shifting paradigms, engaging employees, and dealing with resistance. Consultants also provide essential support to several initiative leaders, ensuring the organization is prepared to face the challenges associated with change.
In conclusion, consulting is essential in implementing a culture of continuous improvement, providing specialized guidance, practical knowledge, and support throughout the process.
The Long-Term Impact of Continuous Improvement
Implementing a culture of continuous improvement can have a significant long-term impact on various vital aspects of organizations. Organizations become more agile, adapting more swiftly to the market, and more resilient, overcoming challenges more quickly and effectively, as experienced in recent years. This results in sustainable business growth.
On the other hand, the constant focus on process optimization, innovation, and problem-solving helps increase operational efficiency, expand production capacity, and win new markets. Additionally, continuous improvement decreases operating costs by eliminating waste, reducing rework, and optimizing resource utilization.
Product quality and customer service also improve. The organization can enhance customer satisfaction by eliminating errors and defects, streamlining processes, and responding more efficiently to customer needs. This leads to greater customer loyalty and the acquisition of new customers through positive referrals.
Lastly, continuous improvement also has a positive impact on employee motivation. By involving everyone in decision-making, problem-solving, and improvement implementation, the workforce feels valued and has the opportunity to contribute to the organization’s success. This results in more motivated and productive employees.
By adopting a culture of continuous improvement, organizations can gain a competitive advantage, achieve consistent results, and successfully adapt to changes in the business environment.
Still Have Questions About Continuous Improvement Culture?
What is a Sustainable Organizational Culture?
A sustainable organizational culture can endure over time, incorporating principles, values, and behaviors consistent with the organization’s vision, mission, and objectives. It’s a lasting culture deeply rooted in the practices and attitudes of its members.
What Does ‘Employee Engagement’ Mean?
Employee engagement refers to the active participation of employees throughout the continuous improvement process. They are encouraged to contribute with ideas, feedback, and solutions to optimize the organization’s processes, products, and services.
What is the PDCA Cycle and the SDCA Cycle?
The PDCA and SDCA cycles are two widely used continuous improvement tools. The PDCA cycle, also known as the Deming cycle or improvement cycle, is a four-step approach consisting of:
- Plan: Plan actions and set clear objectives;
- Do: Implement planned actions;
- Check: Analyze results after implementation;
- Act: Based on verification results, take corrective and preventive actions to improve performance.
The SDCA cycle, also known as the standardization cycle, consists of the following four steps:
- Standardize: Define clear standards for processes or tasks;
- Do: Implement established standards;
- Check: Verify the results of using the defined standards;
- Act: Define corrective actions to address deviations identified during the verification phase.
These cycles are typically used in an alternate and continuous way (PDCA cycle for improvement and SDCA cycle to stabilize the process).
Not Signed Up for Articles and Blogs? Sign Up Now
